Annealing
The annealing process refers to the treatment of a workpiece at a specified temperature, taking into account a defined retention time and subsequent cooling down. A distinction is made between the following annealing processes:
Normal annealing is carried out mainly after a preceding hot forming of components. Heating takes place at a temperature somewhat above the hardening temperature with subsequent cooling in a still atmosphere. The adjustment to a finely-grained perlite-ferrite structure should be achieved by normal annealing. As a result, coarse-grained and irregular structures can be transformed into new homogeneous and fine structures. This type of heat treatment is performed at around 20-50° C above the AC3 transition temperature, at which the austenite-ferrite conversion occurs. Stress-free annealing is used to reduce intrinsic tensions in workpieces incurred by cold forming, structure conversion, thermal wear or machine processing. Stress-free annealing is usually carried out between 450-650°C at sufficiently long retention times and followed by very slow cooling without any significant changes in structure or mechanical properties.
Soft-annealing refers to annealing at a temperature just below the conversion point followed by slow cooling, in order to achieve a soft condition. A granular perlite should result, with a soft microstructure, which gives the optimum workability in non-cutting and cutting processes. This takes place over several hours at just below the AC1 temperature. Annealing on spherical cementite is also a soft-annealing process, using pendular annealing followed by slow cooling in order to achieve a high degree of moulding of its carbides. Here, the aim is a microstructure consisting of cementite grains in a ferritic matrix, and which gives the best working properties. This treatment is of crucial importance for a subsequent cold massive forming, for example.
Coarse-grain annealing, also called high annealing, takes place at a temperature above the hardening temperature with an appropriate cooling to obtain a coarser grain size. The aim of coarse-grain annealing is to improve the machinability of components that are subject to major machining. This occurs at temperatures between 950 and 1200 °C. The retention times must be sufficiently long to achieve the desired grain coarsening. Since grain growth is accompanied by a deterioration of the component properties, the microstructure must be restored to its fine-grain condition in the course of the final stages of heat treatment (hardening, quenching and tempering, case hardening etc.) by phase transformation. Diffusion annealing is annealing at very high temperatures in the recrystallisation zone. The aim is, for example, to partially or fully reverse the changes in properties and structure that arose from cold forming. Diffusion annealing is carried out to compensate the local differences in the chemical composition of steels and cast materials caused by segregation, without any conversion in the microstructure occurring. This happens by annealing in the temperature range of 1000 - 1300 °C.
Solution annealing is principally used for austenite steels to dissolve precipitated constituents in solid solutions and to eliminate tensions incurred by a preceding work hardening. Solution annealing is carried out to achieve uniform and homogeneous microstructural and material properties. In the case of ferrous materials, annealing is carried out in the temperature range between 950 and 1200 °C, and for non-ferrous metals in the range of 460 - 540 °C.
Benefits of annealing
- Improvement of mechanical properties
- Optimisation of mechanical processing (non-cutting and cutting)
- Improvement of the microstructure for cold forming
- Reduction of working and processing tensions
- Restoration of the initial state
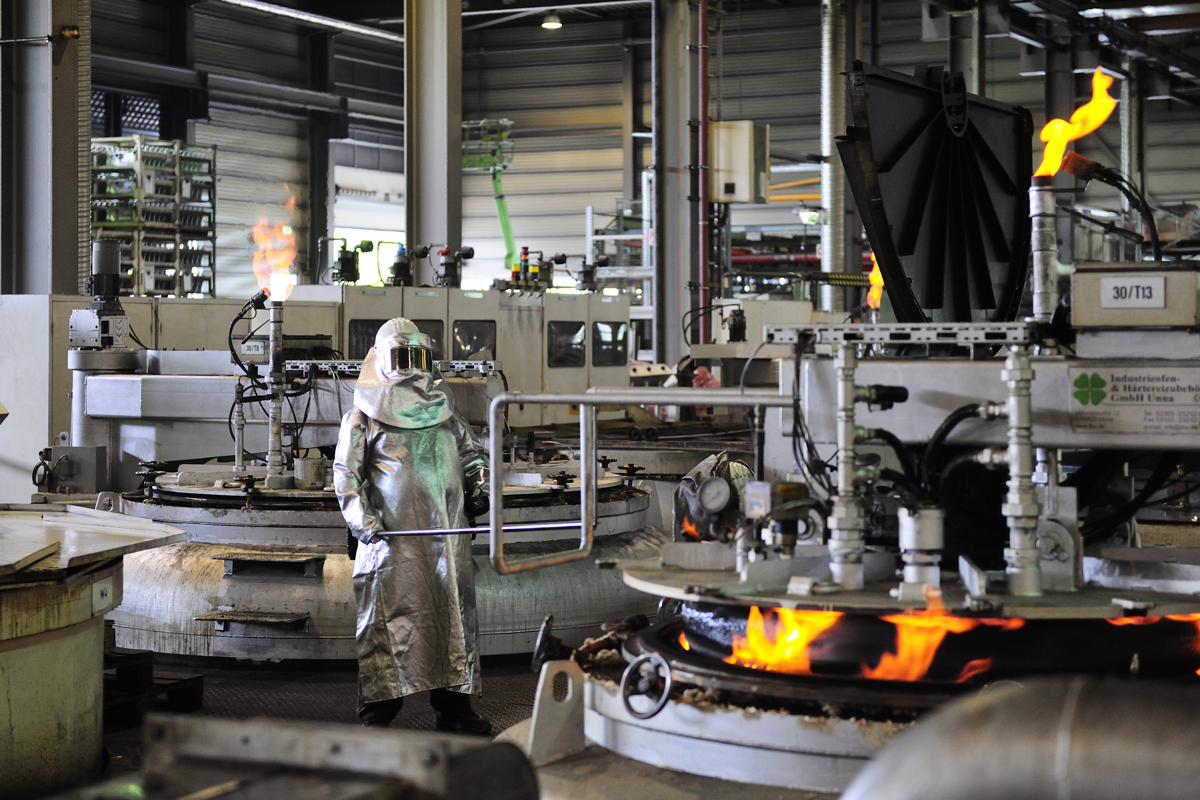