Plasma nitriding / Carburizing
Plasma nitriding is a process which is carried out in a low-pressure atmosphere (vacuum). In plasma nitriding, the component is used as a cathode, and the installation wall serves as the anode. An ionised gas atmosphere results. As a result of the given voltage between the batch and housing, the nitrogen molecules become ionised (glow discharge) and are accelerated towards the workpiece and dissociate on the surface. The nitrogen atoms diffuse into the workpiece and form a hard diffusion zone as well as a corrosion-resistant compound layer on the component surface. Pulsed DC current is used and the component heats up on its own through the process.
In plasma nitriding, loading and process knowledge are crucial for the success of the heat treatment and strongly influence the quality of the final product. With plasma nitriding, the structure of the compound layer can be exactly matched to the respective load profile of the component. The hardness, ductility, corrosion resistance as well as adhesion and abrasion properties can be individually varied and adjusted.
Benefits of plasma nitriding
- Variable compound layer
- Compound layer can be suppressed
- Only slight dimensional and shape changes
- Minimum tolerances
- Environmentally friendly, no toxic side-products
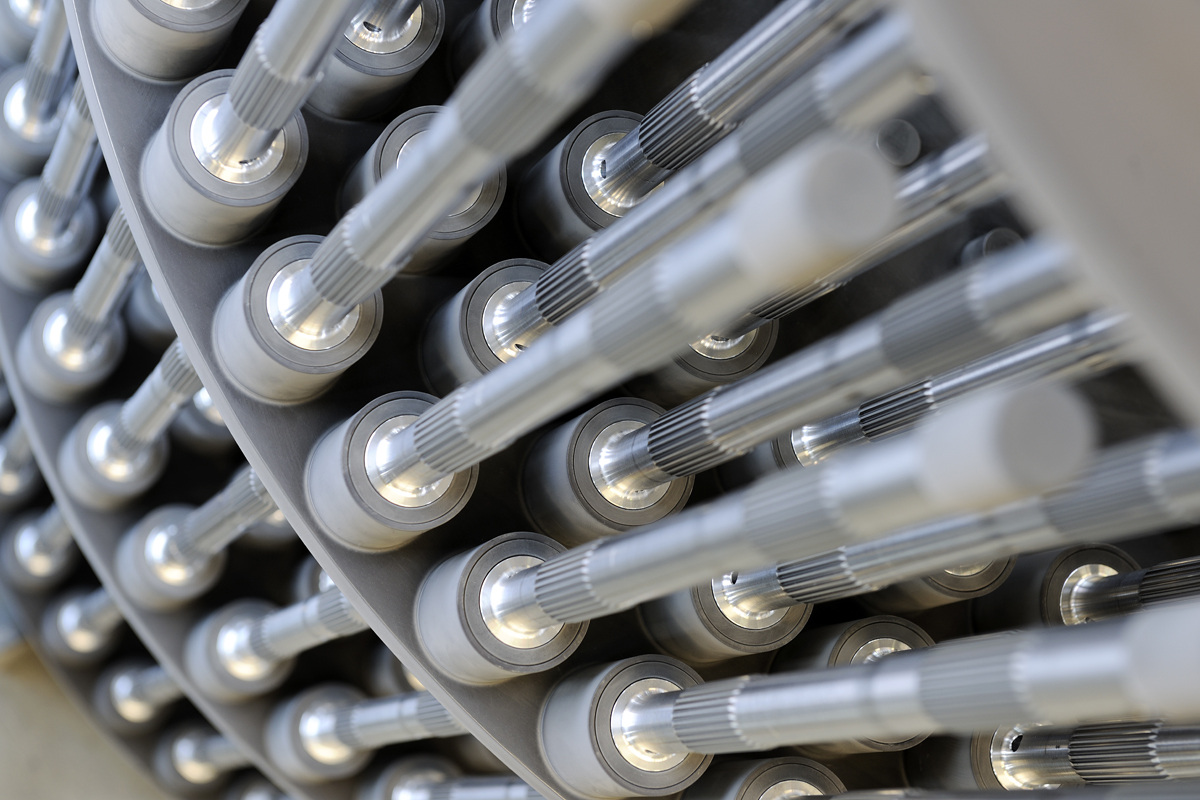