Gas nitriding / Carburizing
During nitriding, the surface layer of a material is enriched with nitrogen. If carbon is additionally diffused in, this is called nitrocarburization.
The process temperatures lie between 480 and 580 °C for nitriding. Depending on the material, the treatment results in a surface hardness of up to 1200 VHN. Due to the relatively low treatment temperatures, no structural conversion takes place, as for example, in hardening. This also explains why only slight dimensional and shape changes occur in nitriding.
The increase in hardness effect is not attained in nitriding by a classical hardening process. The increase in hardness is based on the formation of iron nitrides and special nitrides in the surface layer of the component.
The layer construction is in two parts in nitriding. In the external region it consists of a so-called compound layer with a thickness of 5 -20 µm and comprises almost exclusively iron nitrides. Under the compound layer there is a precipitation zone that supports the compound layer. Here there are special nitrides that cause the increase in hardness. The depth of the precipitation zone correlates with that of the compound layer.
The following general conditions apply for the nitriding process:
The longer the duration of the process, the deeper the nitriding hardness depth and the higher the selected temperature, the deeper the penetration of nitrogen. However, the intrinsic hardness of the nitriding layer diminishes with increasing treatment duration. It requires time, experience and tests to optimally balance these process parameters with the material. The result is subsequently a stable nitriding process with reproducible values.
Benefits of gas nitriding
- Higher wear-resistance
- Only slight dimensional and shape changes
- Stable process
- Regions can be covered that are not to be hardened.
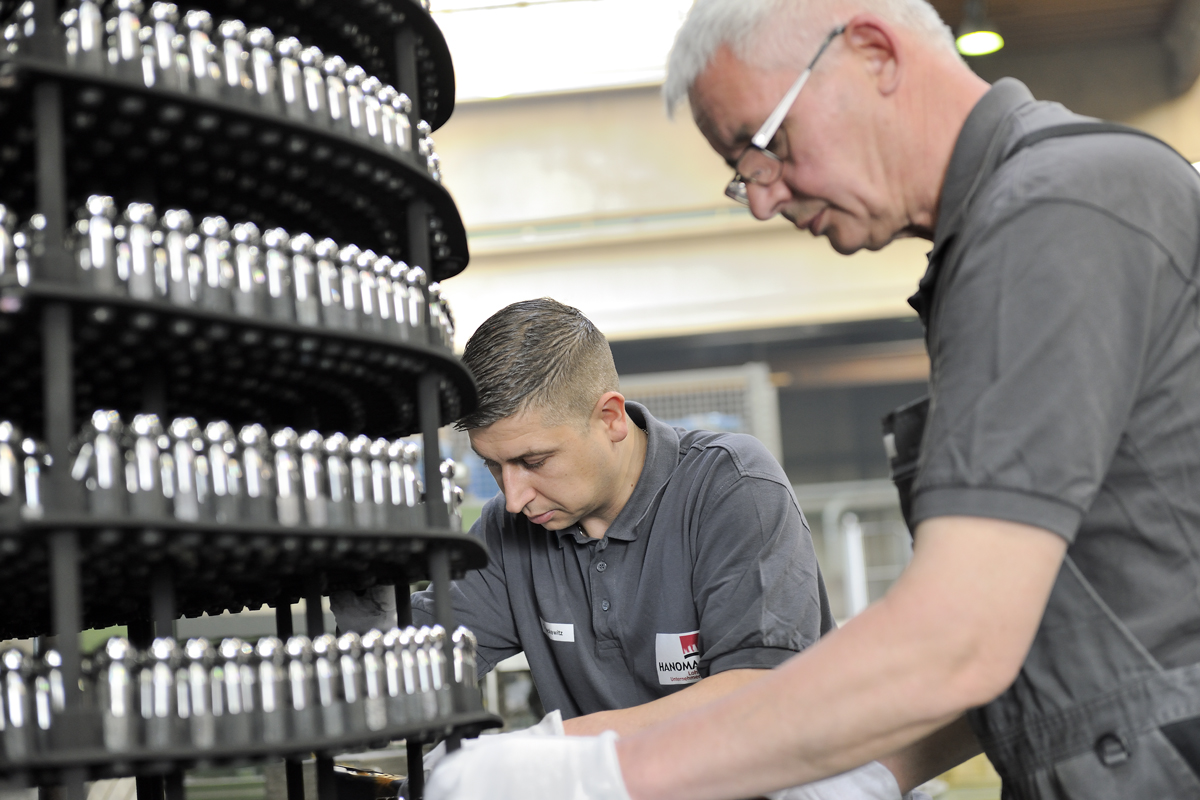